
Tabla 2. Especificaciones de cuatro procesos de manufactura

Tabla 3. Composición proximal de harina de krill sometida a dos procesos de secado

3. Parámetros de referencia
La composición de la harina de krill resulta de la compleja interacción entre la edad, época del año, localización, sexo, condición fisiológica y composición de alimento consumido (Savage y Foulds, 1987).
La composición proximal, expresada en base seca, consiste en 62% de proteína cruda, 13% de extracto etéreo, 7% de fibra cruda, 13% de cenizas y 9% de extracto libre de nitrógeno (tabla 4). Al tratarse de una harina de crustáceos, cuando se habla de proteína cruda se tiene que considerar la participación que tiene la quitina, que en estas harinas, en promedio, es de alrededor del 6%.
El perfil y concentración de aminoácidos de estas harinas cubre los requerimientos para los camarones peneidos siendo una fuente rica en lisina, leucina y arginina (tabla 5).
El krill contiene abundantes proporciones de ácidos grasos poliinsaturados (HUFA por sus siglas en inglés) y una gran parte está compuesta por ácidos grasos omega 3, los cuales se han identificado como esenciales para los camarones (tabla 6). El krill también es una excelente fuente de fosfolípidos, colesterol y astaxantina (tabla 7).
4. Valor alimenticio
La harina de krill es una excelente fuente de proteínas ya que aporta todos los aminoácidos esenciales requeridos por los camarones peneidos; también es un efectivo aditivo ya que funciona como atractante, por lo que se ha utilizado para incrementar la palatabilidad de alimentos con altos niveles de fuentes vegetales y/o de alimentos medicados con antibióticos.
La harina de krill ha sido utilizada como principal fuente de proteínas de alimentos para larvas, juveniles y reproductores de camarones peneidos, con buenos resultados.
Valores expresados como g/100g de lípidos extraídos
La harina de krill, dentro de las harinas de crustáceos, presenta valores relativamente bajos de cenizas (minerales), siendo una buena fuente de calcio y fósforo (tabla 8).
Tabla 8. Contenido de minerales de harinas de krill

(*) valores expresados como g/100 g; (**) valores expresados como mg/kg.
Tabla 7. Contenido de Fosfolípidos, triglicéridos, colesterol y astaxantina de harinas de krill
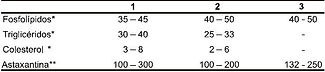
(*) valores expresados como g/100g de lípidos; (**) valores expresados como ppm
Tabla 6. Contenido de ácidos grasos de harinas de krill

Tabla 5. Contenido de aminoácidos de harinas de krill

Valores expresados como g aminoácido/100g de proteína.
Tabla 4. Composición proximal de harinas de krill

Valores expresados como g/100g materia seca.
5. Consideraciones generales
La mención de marcas comerciales en el presente documento no implica ningún tipo de recomendación.
Las harinas krill contienen muy bajos niveles de contaminantes como dioxinas, PCB y metales pesados, lo cual esta relacionado a que provienen de aguas no contaminadas (Sclabos y Toro, 2003).
En la actualidad, el principal uso de la harina de krill es más como aditivo alimentario que como fuente de proteínas.
4.1 Inclusión en la dieta
Tabla 9. Respuesta de los camarones peneidos a la inclusión de harina de krill en el alimento
